Day :
- GMP in Food Industry | Current GMP Guidelines (cGMP) | Quality Assurance | Quality Control | Clinical Affairs & Regulatory Strategies Implementation”
Location: Doubletree by Hilton Chicago North Shore
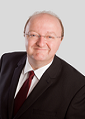
Chair
Paul J Cummings
PJC Pharma Consulting Ltd, UK
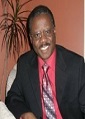
Co-Chair
Felix Amiri
Global Coalition for Sustained Excellence in Food & Health Protection (GCSEFHP), Canada
Session Introduction
Felix Amiri
Global Coalition for Sustained Excellence in Food & Health Protection (GCSEFHP), Canada
Title: Food industry Good Manufacturing Practices (GMPs) and the Safety, Security and Quality Assurance (SSQA) concept
Time : 11:20-11:40
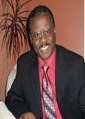
Biography:
Felix Amiri is the current food sector Chair of the Global Coalition for Sustained Excellence in Food & Health Protection (GCSE-FHP). He is a key contributor to the Safety, Security and Quality Assurance (SSQA) concept implementation manual published by Amiri Food Industry Support Services (AFISS). He also teaches International Food Safety Law and Regulations at Conestoga College. He has an in-depth knowledge of food safety and quality management systems. With more than 30 years of industry experience and an extensive knowledge of international standards, he serves as the Technical Director at AFISS, where he provides consulting services to various food companies. He also conducts system management and regulatory audits with SAI Global. Prior to his current role at AFISS, he worked in product development and quality management roles with various reputable companies, including Vese Food (Nigeria) Ltd., Unifine Richardson, Golden Valley Farms, Heinz (Martin Pet Foods) and YUM Brands.
Abstract:
The food industry has seen the adoption of different concepts and strategies for ensuring controlled and efficient implementation of GMPs. The evolution has continued from periods of no formalized systems to the introduction of highly sophisticated manufacturing management models. Many food companies have adopted well-known concepts such as: Total Quality Management(TQM); Strength, Weakness, Opportunity, Threat (SWOT) analysis; Failure Mode and Effects Analysis (FMEA) models; 6-S systems; Statistical Process Control (SPC); Statistical Quality Control (SQC); Six Sigma; Kaizen Methodologies; Lean Manufacturing; International Standards Organization (ISO) system; Hazard Analysis and Critical Control Point (HACCP) system; Global Food Safety Initiative (GFSI) Benchmarking system; et cetera. The overwhelming number of concepts has forced food companies to adopt them exclusively and in isolation. This creates both the necessity and the opportunity for the adoption of a synergy-building concept like SSQA. The SSQA model is a focused approach to managing GMPs, product safety, security and quality. The SSQA concept actively drives operations to search, recognize, investigate, adopt and expand upon winning ideas drawn from excellence-producing management approaches. The SSQA model is didactic, eclectic, organic and progressive. It brings together the theory and reality of product safety, security and quality assurance. SSQA directly and actively drives a collaborative engagement of all parties involved in the material supply, processing, distribution, utilization, regulation and independent assessment of operations with tools for ensuring and measuring success. Through a six-step implementation strategy, SSQA draws from other useful concepts and ensures resource utilization efficiency; effective implementation of programs, procedures and actions through the entire chain engagement process; team mobilization strategy; the tracking of exceptional success; failure analysis and control tracking; continuous analysis of realized effectiveness and efficiencies; and a HACCP system that addresses difficult-to-manage situations.
Sharmeen Reza
Cytel Statistical Software and Services Private Limited, India
Title: Quality control in statistical programming under GCP
Time : 11:40-12:00

Biography:
Sharmeen Reza is the Director of Statistical Programming at Cytel Inc., a major functional service provider for pharmaceutical and biotech companies. Previously, she was the Biostatistical Programming Manager at Amgen. She has 20+ years of clinical background. On many occasions she gave presentations on quality control, trained new hires and helped them come up to speed. She has presented papers at conferences emphasizing the nature of collaboration in R&D and discussing statistical programming solutions.
Abstract:
Statistical programming to support clinical research and data analysis is vital in the drug discovery process. GCP is a prerequisite for any submission to regulatory authorities for drug approval and licensing. Quality control (QC) comes with different measures and tools following Standard Operating Procedures (SOPs), established by sponsor companies and/or Contract Research Organizations (CROs). The SOPs are mainly based on GCP guidelines. This presentation exhibits brief overview of QC in overall clinical trials, with focus on QC done right for statistical programming in a R&D environment. It gives relevant definitions, processes followed, reasons for QC, challenges faced, deviations and expectations. The topic also describes roles, expertise, requirements, documentation and responsibilities involved. Given a drug’s prospects, the impact of a solid QC process outweighs resource investments. Since quality is a key performance indicator and helps to select preferred partnership, pharmaceutical companies highly value CRO capabilities in conducting QC.
Chris Wubbolt
QACV Consulting LLC, USA
Title: Data integrity requirements for GxPs
Time : 12:00-12:20
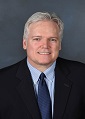
Biography:
Chris Wubbolt has provided quality assurance, compliance, and computer validation consulting services since 2001, specializing in establishing data integrity programs, performing data integrity audits, vendor audits, providing training, validation, and implementing six sigma based quality improvement processes. He has previously worked at Aventis Pasteur as Computer Validation Manager, working with GxP computerized systems. Prior to joining Aventis Pasteur, he worked at Johnson & Johnson’s McNeil Consumer Products Company in the National Quality Assurance Group and at Lancaster Laboratories. He was a contributing member of the GAMP Laboratory Systems Special Interest Group, which published the guidance document on validation of laboratory systems, as well as a chapter chair for DIA “Peach” guidance on computerized systems used in clinical research. He is a Certified Six Sigma Black Belt, has a Master’s degree in Quality Assurance and Regulatory Affairs and a BS in Physics and Computer Engineering. He was the previous President of both the New England Region Chapter Society of Quality Assurance (NERCSQA) and the Mid-Atlantic Region Society of Quality Assurance (MARSQA), and is currently the chairperson of the MARSQA computer validation committee.
Abstract:
This presentation will provide an overview of current regulatory requirements and guidance pertaining to data integrity. The presentation will review FDA, MHRA and other regulatory guidance related to data integrity. Approaches to performing data integrity assessments will be discussed and examples from audits and regulatory observations will be reviewed. Implementation of data integrity programs will also be reviewed. The following topics will be discussed at the conference: Review current regulatory data integrity requirements and guidance; approaches to conduct audits / assessments of data integrity programs; examples of data integrity observations and audit findings and; implementing data integrity programs.
Mayra Guzman-Kaslow
GK Regulatory, Compliance, & Engineering Consulting Corporation, USA
Title: Regualtory compliance & notified bodies inspection readiness
Time : 12:20-12:40
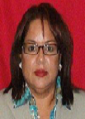
Biography:
Mayra has two BS, (1) in Chemistry, and (2) in Chemical Engineering from the University of Puerto Rico, and a Master of Sciences, in Thermodynamics and Materials Sciences Engineering from the University of Cincinnati, OH. She is the President of GK Regulatory Compliance Corp., and the Chairman of GK Bio-Pharmaceuticals CMO - PR a premier Bio-Pharmaceuticals Contract Manufacturing Organization locaded in Vega Baja, PR. She has a track-record of accomplishment for consistently meeting goals and delivering a high level sustained performance, proven the ability to build strong customer/client relationship including conducting vendor audits and contract manufacturing oversight. She has been a key element in the Regulatory Compliance Readiness for Major Pharmaceuticals, APIs, Biotech, Biosimilars, CMOs.
Abstract:
“Inspection Readiness” is a site-preparation activity often done in anticipation of an upcoming third party audit, due diligence activity, FDA inspection, Notified Body inspection, or other Regulatory Agency inspection. FDA inspectors have a limited amount of time at a facility to gather a large amount of data and evaluate your respective product/facility/quality system. Similarly, pharmaceutical companies have a limited amount of time to make a positive impression with the inspection team, convey relevant information, and ensure a favorable outcome. Inspection Readiness is the best way to prepare for an onsite inspection. Inspection Readiness is not typically an activity that is done internally. Having an outside perspective is a critical component to effectively evaluating your quality systems, facilities, and personnel. Inspection Readiness is one of the best ways to utilize an outside resource. Experienced consultants that have worked with a variety of companies will give the best perspective. FDA inspections are assigned for many different reasons. Safety (risk to health) plays a major role in how FDA selects firms for inspections. Firms can estimate their likely risk status in terms of FDA’s regulatory interest. Once a firm is selected for inspection, how the inspection is conducted becomes a make-or-break situation. Inspections are designed to find problems. They are inherently uncomfortable for the people who host the investigator during the inspection. Predicting what an investigator will do during an inspection becomes helpful in how you manage a difficult situation to avoid a potentially disastrous and costly result. In order for Inspection Readiness to be effective, it must be objective and have the full support of senior management.
Rashid Mehmood
Surge Laboratories Private Limited, Pakistan
Title: Quality risk management system
Time : 12:40-13:00
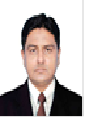
Biography:
Rashid Mahmood has a Master’s degree in Analytical Chemistry and MS in Total Quality Management. He has 13 years of experience in Pharmaceutical Quality Operations and has attended many international conferences as a keynote speaker. He has presented various talks in USA & China on Cleaning Validation, cGMP Guidelines and Quality Risk Management. Currently, he is working as a Senior Executive Manager Quality Operations for Surge Lab (Manufacturer of Microencapsulated APIs, Liquid & Dry Powder Parentrals) which is the best export oriented company in Pakistan.
Abstract:
In the pharmaceutical industry every product and every process will be associated with risks. To maintain product quality throughout the product life cycle, too much time and resources are allocated. Risk is described in – recent guidance as a combination of the probability of occurrence of harm and the severity of that harm. The Quality Risk Management (QRM) approach initiated by regulatory agencies with recognized management tools along with support of statistical tools in combination allows for a risk based approach to quality management, thus ensuring that resources are deployed in a timely and expeditious manner to areas that need them most. QRM improves risk awareness and accelerates detection of potential issues by analyzing and comparing existing data from a quality perspective to manage product quality, manufacturing processes, validation and compliance within a risk based Quality Management System. In addition quality risk management improves decision making if a quality problem arises. It should include systemic processes designated to co-ordinate, facilitate and improve science based decision-making with respect to risk. Quality Risk Management can be applied not only in the manufacturing environment, but also in connection with pharmaceutical development and preparation of the quality part of marketing authorization dossiers. The guideline applies also to the regulatory authorities in the fields of pharmaceutical assessment of the quality part of the marketing authorization dossier, GMP inspections and the handling of suspected quality defects. ICH Q9 - Quality Risk Management provides an excellent high level framework for the use of risk management in pharmaceutical product development and manufacturing quality decision making applications. It is a landmark document in acknowledging risk management as a standard and acceptable quality system practice to facilitate good decision-making with regard to risk identification, resource prioritization and risk mitigation / elimination, as appropriate
- Quality Assurance | The Role of c in cGMP | Current GMP Guidelines (cGMP) | Validation
Location: Doubletree by Hilton Chicago North Shore
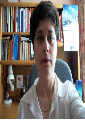
Chair
Eleonora Babayants
Galaxy Consulting, USA
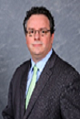
Co-Chair
Paul Lopolito
STERIS Corporation, USA
Session Introduction
Paul Lopolito
STERIS Corporation, USA
Title: Cleaning validation: Process life cycle approach
Time : 10:30-10:50
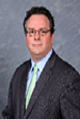
Biography:
Paul Lopolito is a Technical Services Manager for the Life Sciences Division of STERIS Corporation (Mentor, Ohio). He currently provides global technical support related to process research cleaners, stainless steel maintenance, and contamination control, which includes field support, site audits, training presentations and educational seminars. He has over 15 years of industry experience and has held positions as a technical services manager, manufacturing manager and laboratory manager. He is a frequent speaker at industry events including INTERPHEX, PDA, ISPE, ACHEMA, AALAS, and IVT. He has published several articles and book-chapters related to cleaning validation and contamination control. He earned a BA in Biological Sciences from Goucher College in Towson, MD.
Abstract:
The traditional cleaning validation approach has been used for over thirty years to define and validate manual and automated cleaning within GMP manufacturing. The life cycle approach includes three stages, (1) process design, (2) performance qualification and (3) continued process verification. The cleaning life cycle approach changes the emphasis from validation to design and monitoring of the cleaning process. Monitoring of the cleaning process and a better understanding of the design process (critical parameters) promotes continuous improvements and real-time scientific based decisions to OOS results and change management. Industry tools such as QbD, risk management and PAT provide the backbone to the life cycle approach. The easy-to-follow presentation provides a checklist for any organization to successfully migrate from a traditional validation model to the cleaning life cycle approach for new products or processes. The presenter will also cover some hot topics within cleaning validation, such as establishing health based limits, visual inspection, addressing non-routine cleaning residues and stainless steel maintenance.
Sudhakar Sagaram
BDR Pharmaceuticals Internationals Pvt. Ltd., India
Title: Develop and implement effective methods of teaching and convenient procedures for the implementation of new methodology student centered learning to drive the institute to new heights by satisfying more and more students and industrial needs
Time : 10:50-11:10
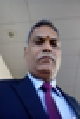
Biography:
A competent professional with years of industrial and Academic experience with years as executive level and in senior level of experience in Quality Assurance, Consultancy, Regulatory Affairs, Production scale up and Technology Transfer in the Pharmaceutical Industry. Expertise in carrying out various inspections, audits, and review for processes release of quality standards of goods. Proficient in managing all documentation / paperwork to ensure accuracy as per regulatory requirements.
Abstract:
The documentation play very important role in the present global pharmaceutical sector. This acts as barrier between all the segments of business development .Hence most of the pioneer organizations of this sector prefer to have a team of professionals to handle this activity with strong background of regulatory and process related knowledge. In the pioneer organizations this activity is handling through electronic media. But 80% of the pharmaceutical industries in India are not having the software knowledge and its applications in this regard. The present attempt is to establish and define an internal effective documentation program to ensure the competency of personals to Design, Develop, Digest, Execute, Life Cycle Management and Archive of documentation modules. Through develop and implement methods of training and convenient procedures for the implementation of documentation through new methodology of personal centered learning to drive the organizations to new heights by executing the strong documentation system which meets the requirements of regulatory bodies , easily ,effectively executable and affordable by the organizations.
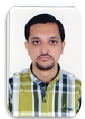
Biography:
Chintan V Pandya has his expertise in Quality Control and Validation since last several years. He worked as a Research Associate in research institutes as well as in many industries. He has developed and validated many methods after years of experience in research, evaluation, teaching and administration both in pharmaceutical industries and education institutions. He is the Head and Professor of Chemistry at HVPGR, Kadi – KSV (India). He has an excellent track record in academics at an institution of high repute, in research with more than 10 international research articles and presented his work in national and international conferences. He has published more than 15 research articles and books in reputed and peer reviewed journals and publications. He also associated as reviewer and Editorial Board Member with many reputed publications.
Abstract:
Quality control is defined as the analysis of an intermediate model to identify aspects that are unusual in some sense and that could, therefore, be a result of errors in the model building or refinement process. Any such errors need to be fixed, if possible, prior to analysis and publication of the model. Validation is the process of assessing the reliability of the final model that is about to be analyzed, published, deposited, and possibly used in follow-up studies. Quality Control is known as QC and focuses on identifying defect. QC ensures that the approaches, techniques, methods and processes are designed in the project are following correctly. QC activities monitor and verify that the project deliverables meet the defined quality standards.
Quality Control is a reactive process and is detection in nature. It recognizes the defects. Quality Control must complete after Quality Assurance. A simple, rapid, accurate and sensitive method was developed for quantitative analysis. The method showed adequate precision, the method was validated for the parameters like specificity, linearity, precision, accuracy and robustness. Accuracy is one of the most important parameters of an analytical methodology and it can be expressed as the percent recovery of known amounts of drug added to a sample. The precision refers to the variability of the results in repeated analyses of the sample under identical experimental conditions. The method was validated by evaluating the intra- and inter-day precision. The precision was calculated from an average of ten determinations of a homogeneous sample.
Andrea Geyer,
Universidade de Brasilia, Brazil
Title: GMP deficiencies found by ANVISA in foreign inspections
Time : 12:00-12:20
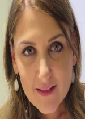
Biography:
Andrea R C Geyer has worked for ANVISA as an Inspector since 2005. She is an Industrial Pharmacist and has completed her MSc in Biological Sciences (Biochemistry). Currently, she is pursuing her PhD in Pharmaceutical Sciences at Brasilia University, studying the most common deficiencies found during ANVISA inspections.
Abstract:
Statement of the Problem: Good Manufacturing Practices (GMP) main objective is managing and minimizing the risks inherent in pharmaceutical manufacture to ensure the quality, safety and efficacy of products. Pharmaceutical manufacture and regulation is an international business. Regulatory authorities and the pharmaceutical industry are seeking for maximum harmonization of GMP guidelines. The main objective of the present study is to evaluate the results of Brazilian Health Regulatory Agency (ANVISA) foreign inspections in the last two years (2015 and 2016), comparing with other regulatory authorities.
Methodology & Theoretical Orientation: Results were collected from a total of 255 inspection reports. The result of the inspection was grouped by company compliance status and country. The number and criticality of deficiencies were collected and grouped by area, according to current GMP regulation in Brazil. Deficiencies found more often were listed descriptively. In the period evaluated, 63.14% of ANVISA inspected companies were classified as satisfactory, 25.88% resulted in demand status and 12.55% of inspections concluded that the company did not comply with GMP (Unsatisfactory). In 19 inspections (10.16%), critical deficiencies were found; inspectors observed major deficiencies in 111 (59.36%); and minor deficiencies were observed in 165 (88.24%) of the inspected companies. The most common areas of deficiency were documentation (28.63%) and Premises (26.27%).
Conclusion & Significance: The pattern of deficiencies was like the findings of other regulatory agencies, showing that equivalent requirements are applied. Disclosure of the common deficiencies is a step forward on regulatory transparency, which can be useful for industry to improve GMP compliance. Therefore, producers are encouraged to allocate resources and training on these main issues, assuring quality and safe medicines supply for population.